OEM Aluminum Alloy Adjustable Towing Hitch for Trailer Accessories Hot Forging Parts
- Packaging:
- Standard export packing or according to customers' specifict requirments.
- Supply Ability:
- 10 Pack/Packs per Day
- Port:
- Qingdao Port
Product Description
Product Show
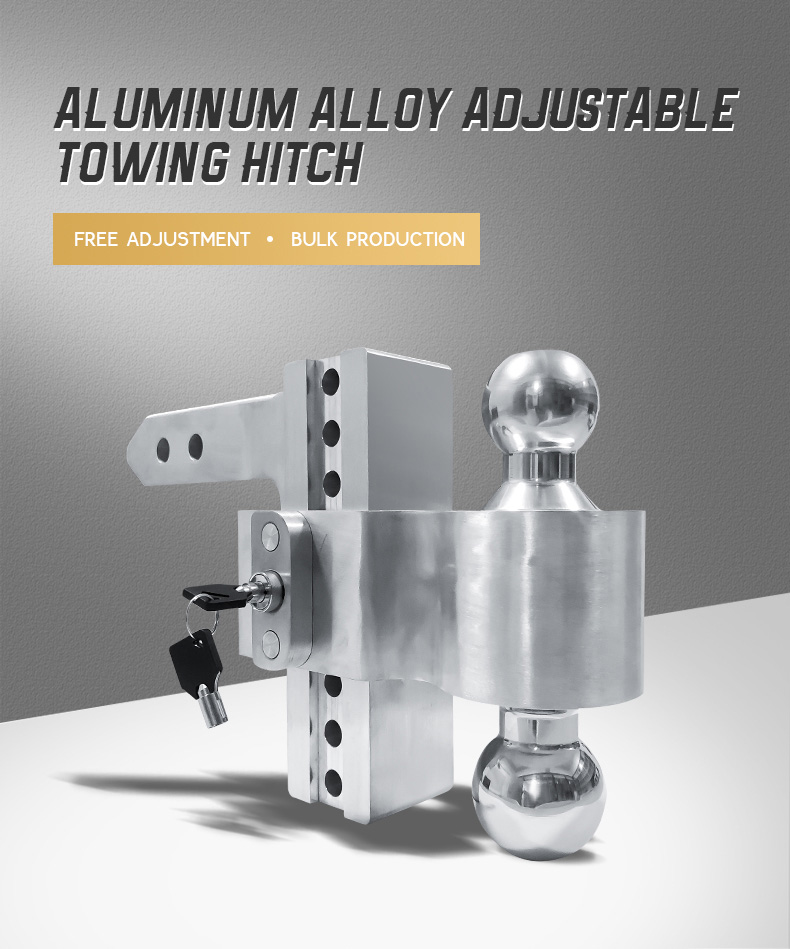
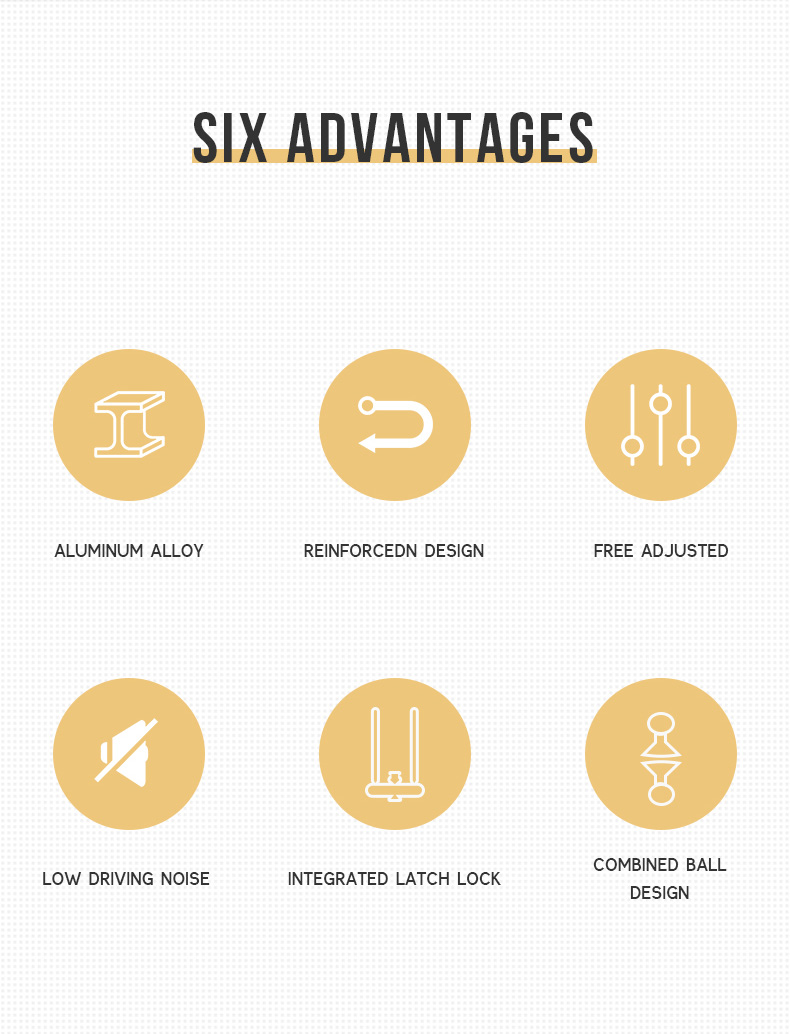
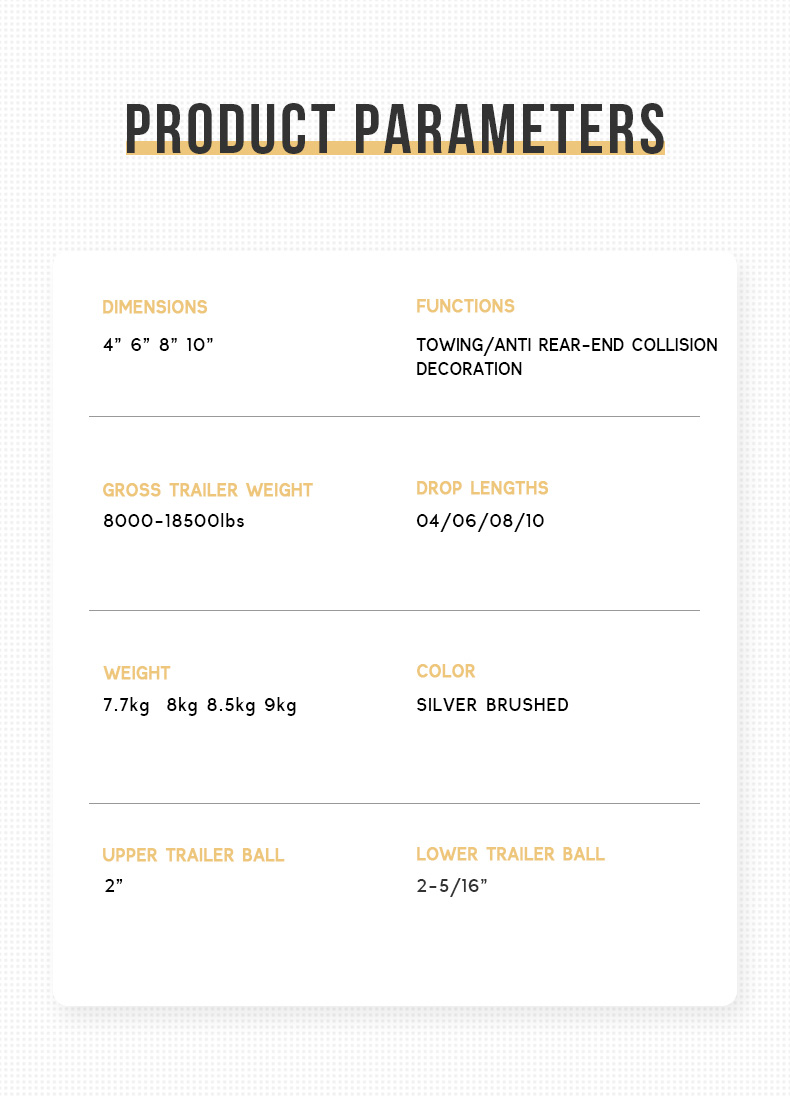
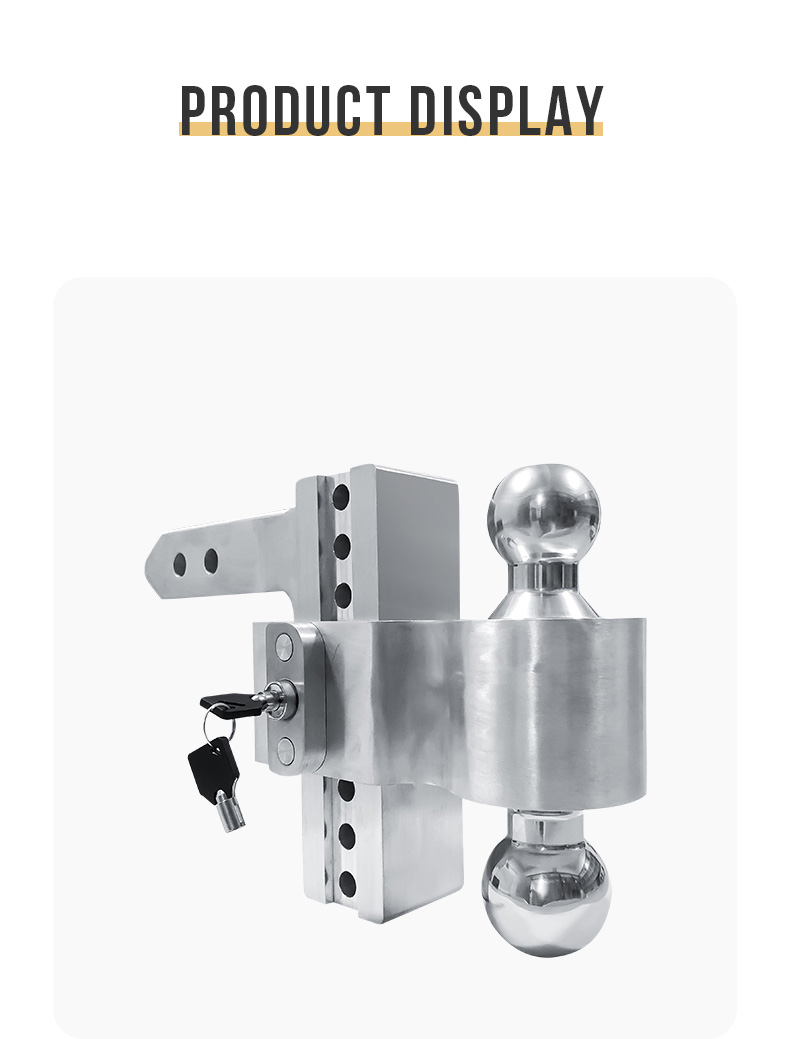
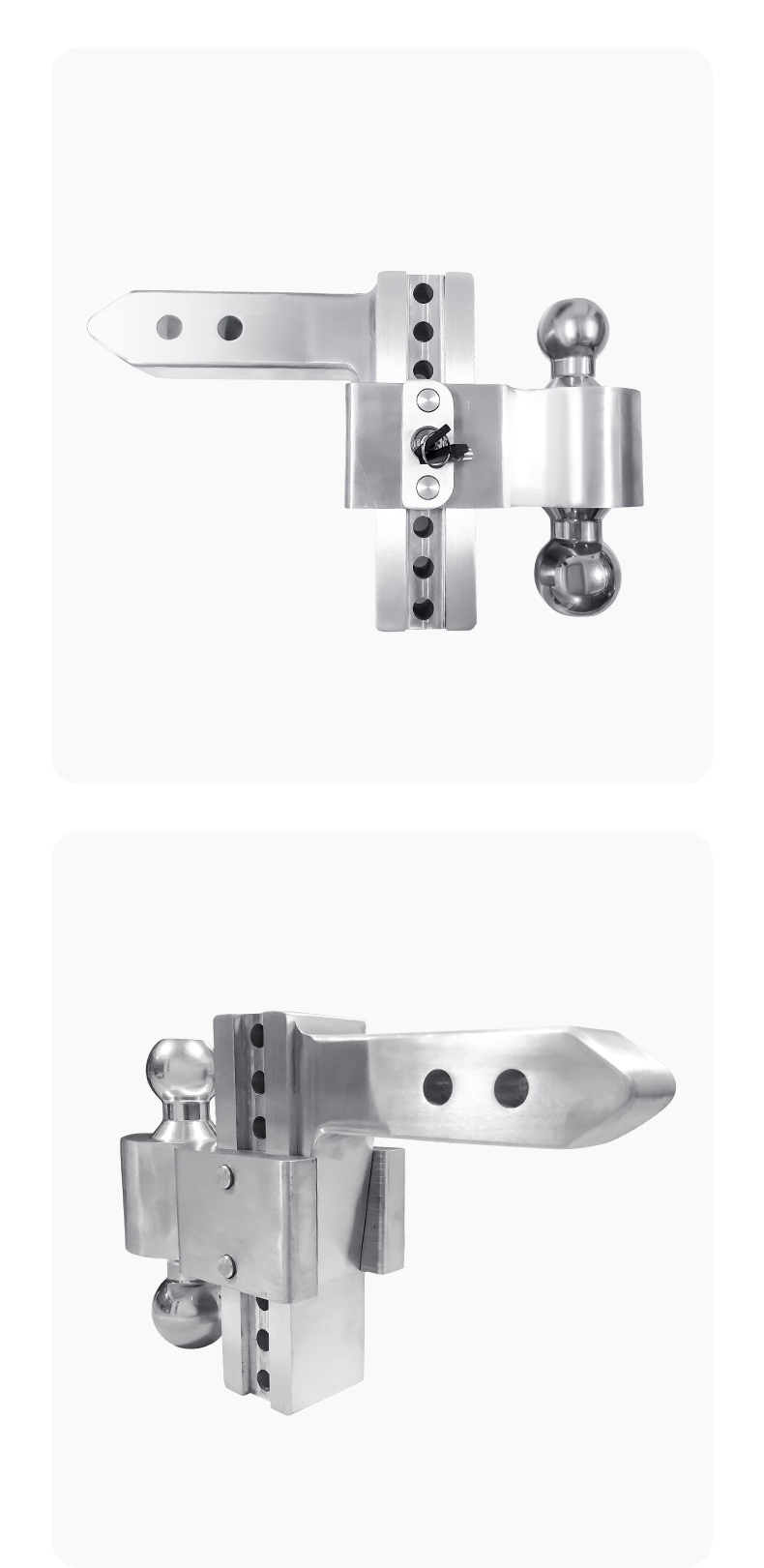
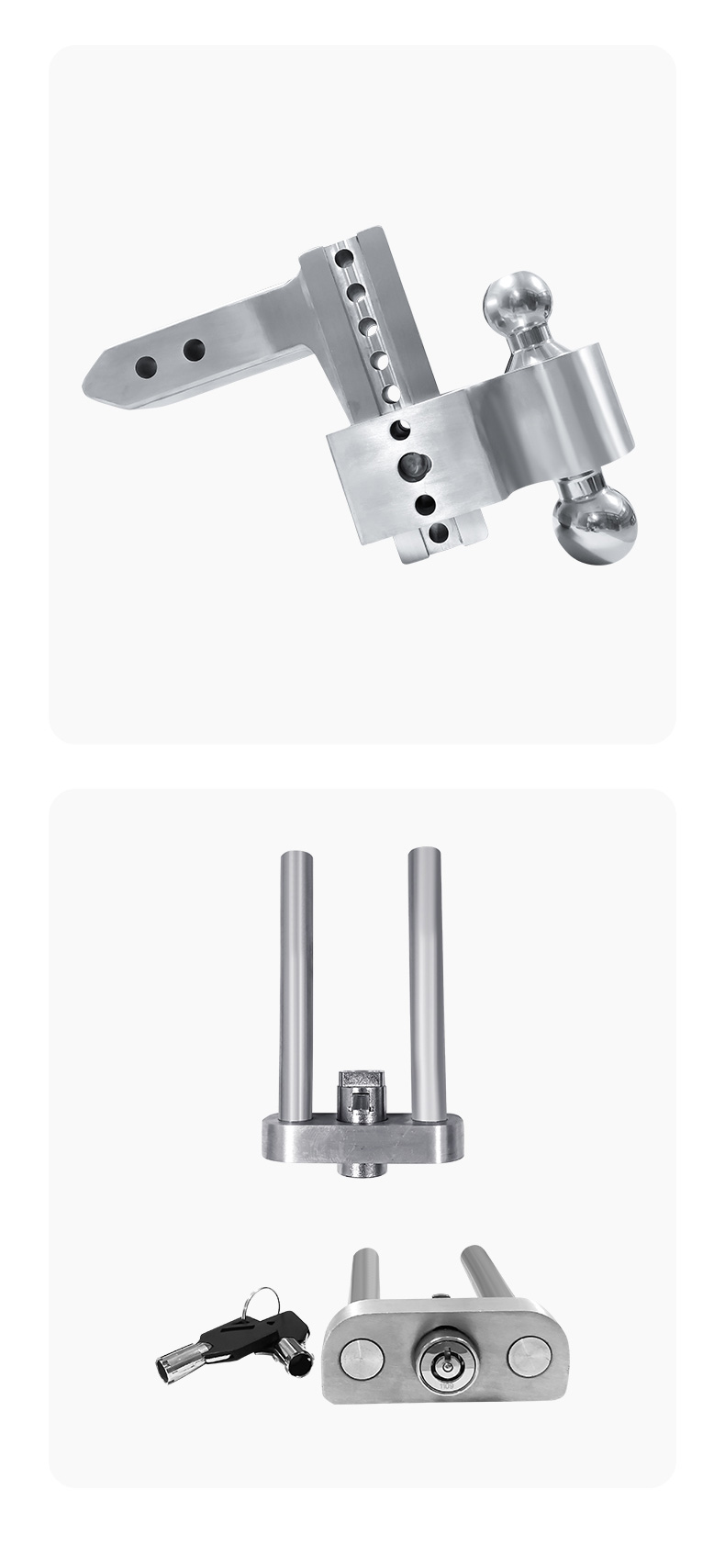
Product Name | OEM Aluminum Alloy Adjustable Towing Hitch for Trailer Accessories Hot Forging Parts |
Dimensions | 4" 6" 8" 10" |
Functions | TOWING/ANTI REAR-END COLLISION/DECORATION |
Gross Trailer Weight | 8000-18500lbs |
Drop Lengths | 04/06/08/10 |
Weight | 7.7kgs/8kgs/8.5kgs/9kgs |
Color | Sliver |
Upper Trailer Ball | 2” |
Lower Trailer Ball | 2-5/16” |
Company Profile
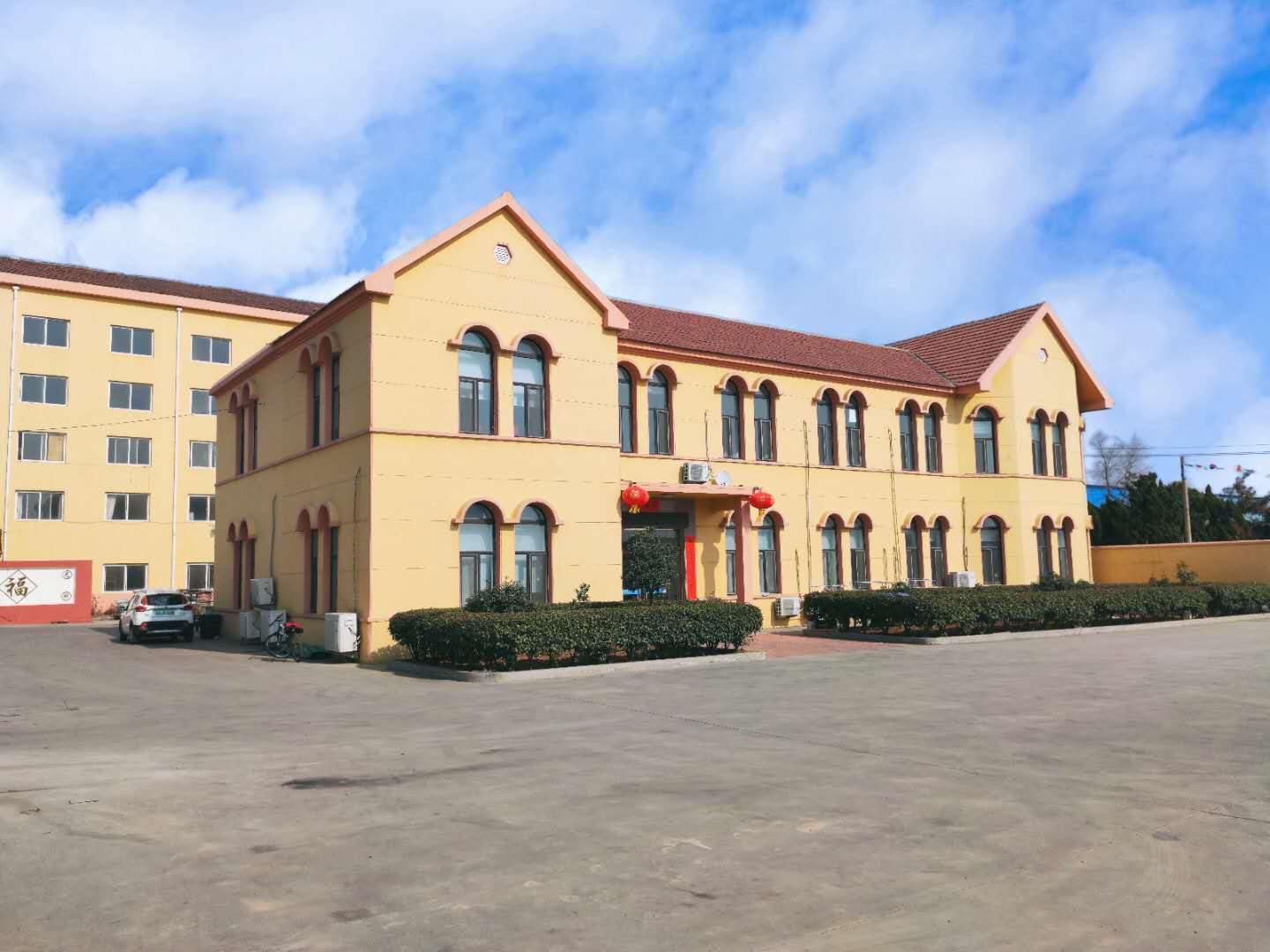
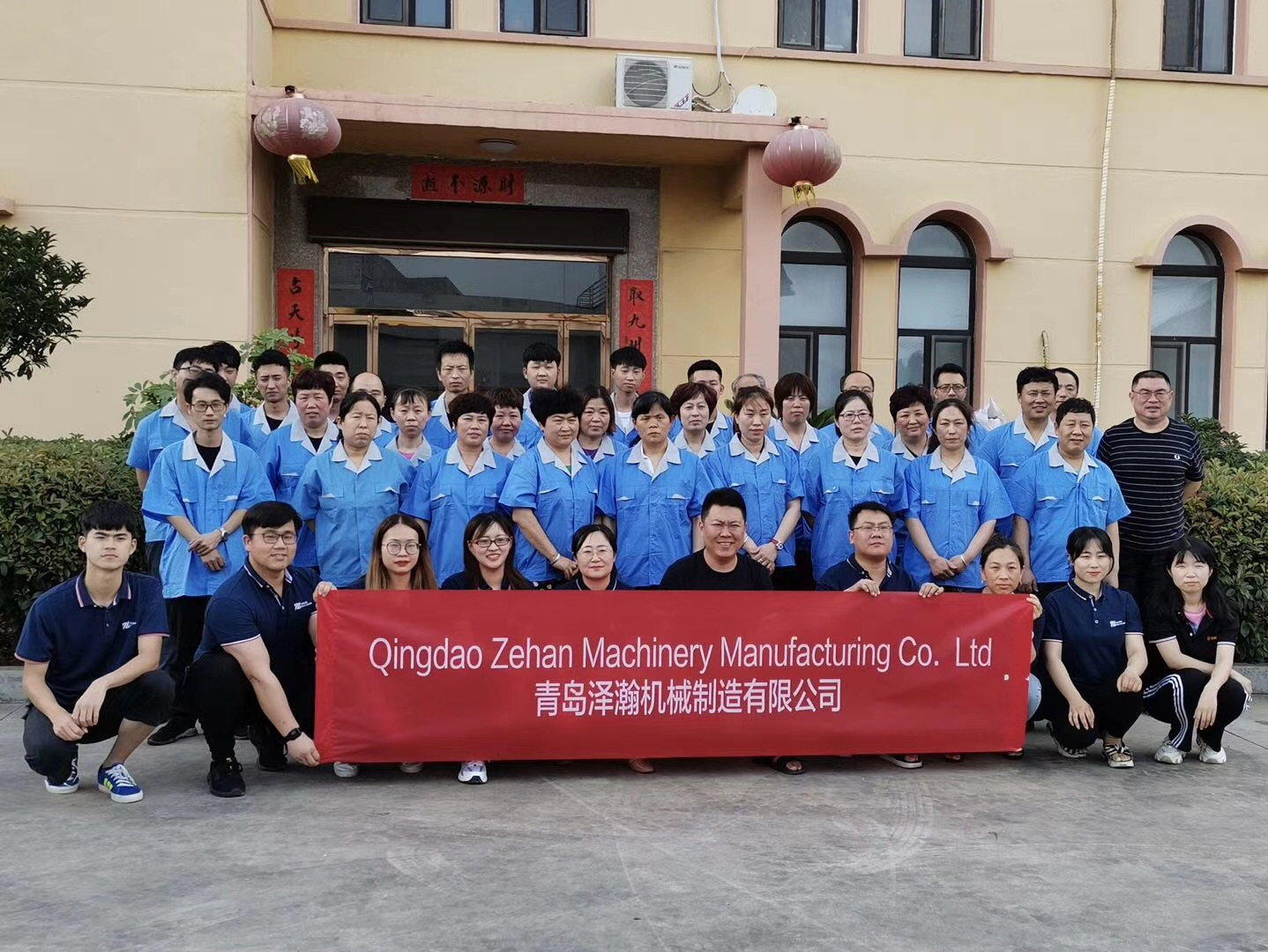
Qingdao Zehan Machinery Manufacturing Co., Ltd is an export-oriented high-tech enterprise specializing in fabrication of high-end metal parts, keeping a long-term and stably strategic cooperation with a number of world-famous enterprises since 2006. Our products are widely used in precision equipment, engineering machinery, construction, power facility, medical, animal husbandry, aviation, rail traffic and other industries. They have been widely sold in high-end market like North American and European countries. Zehan has more than 60 sets of equipment, specializing in automatic lathes, CNC lathes and CNC Machining center. Besides, our factory is equipped with 20 sets air hammer and punching machine respectively. Providing precision & durable components, Qingdao Zehan Machinery Manufacturing Co., Ltd has a strong focus on employing advance manufacturing facilities like 5 axis CNC machining centers, 3D printing machines, which could ensure highest quality and reliability of components at our own production facilities. Qingdao Zehan Machinery Manufacturing Co., Ltd. sincerely welcomes more friends to cooperate with us, and create a better future together.
Machining Equipment
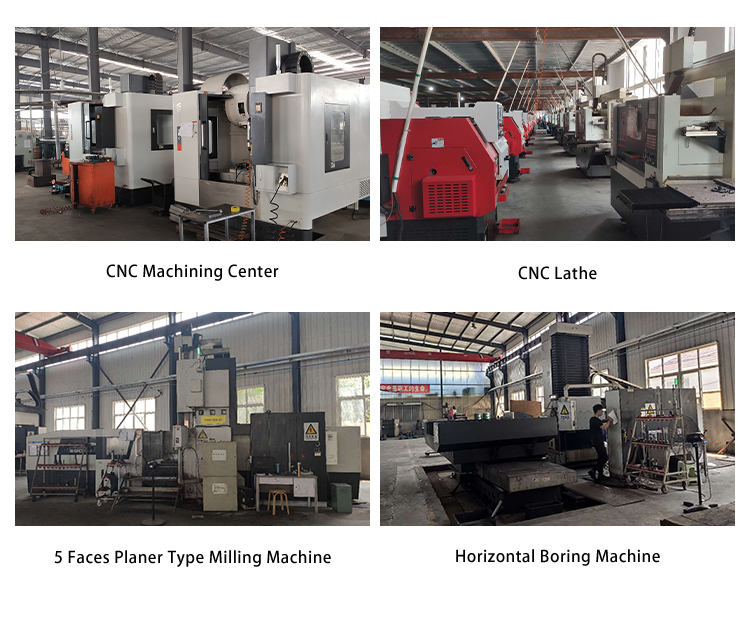
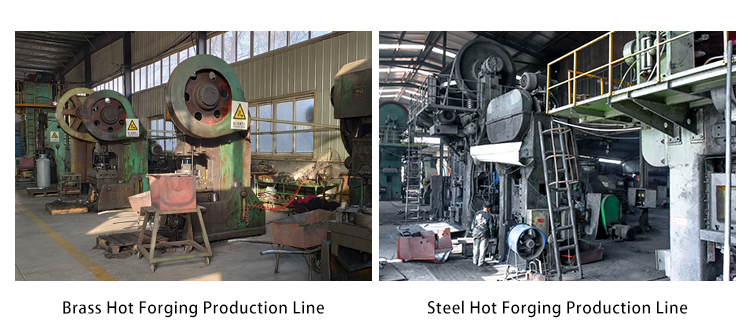
Testing Equipment
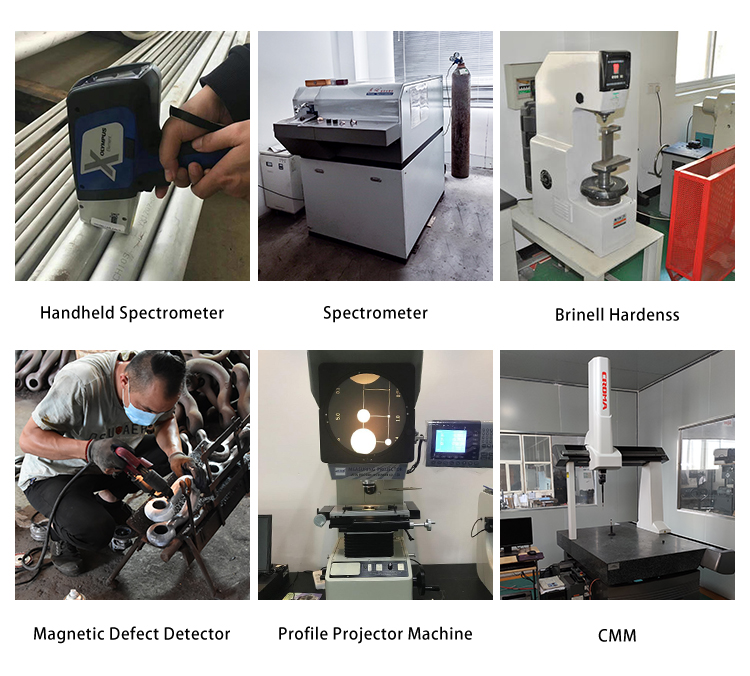
Manufacturing Process
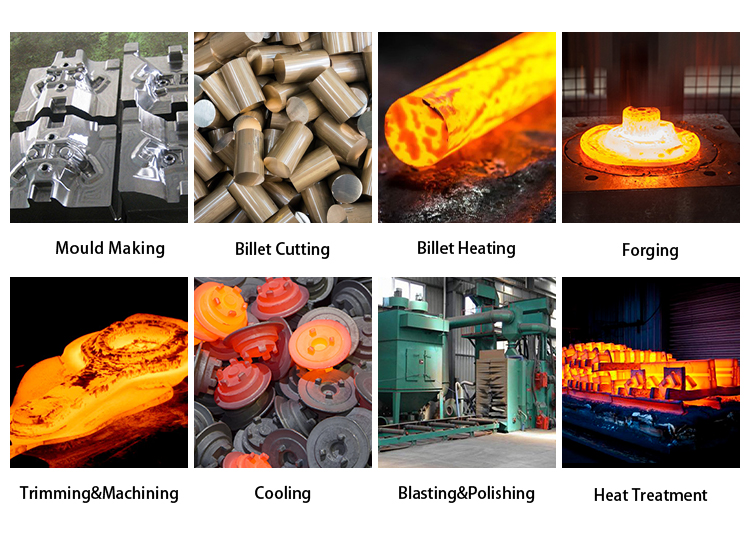
Customers VIsiting
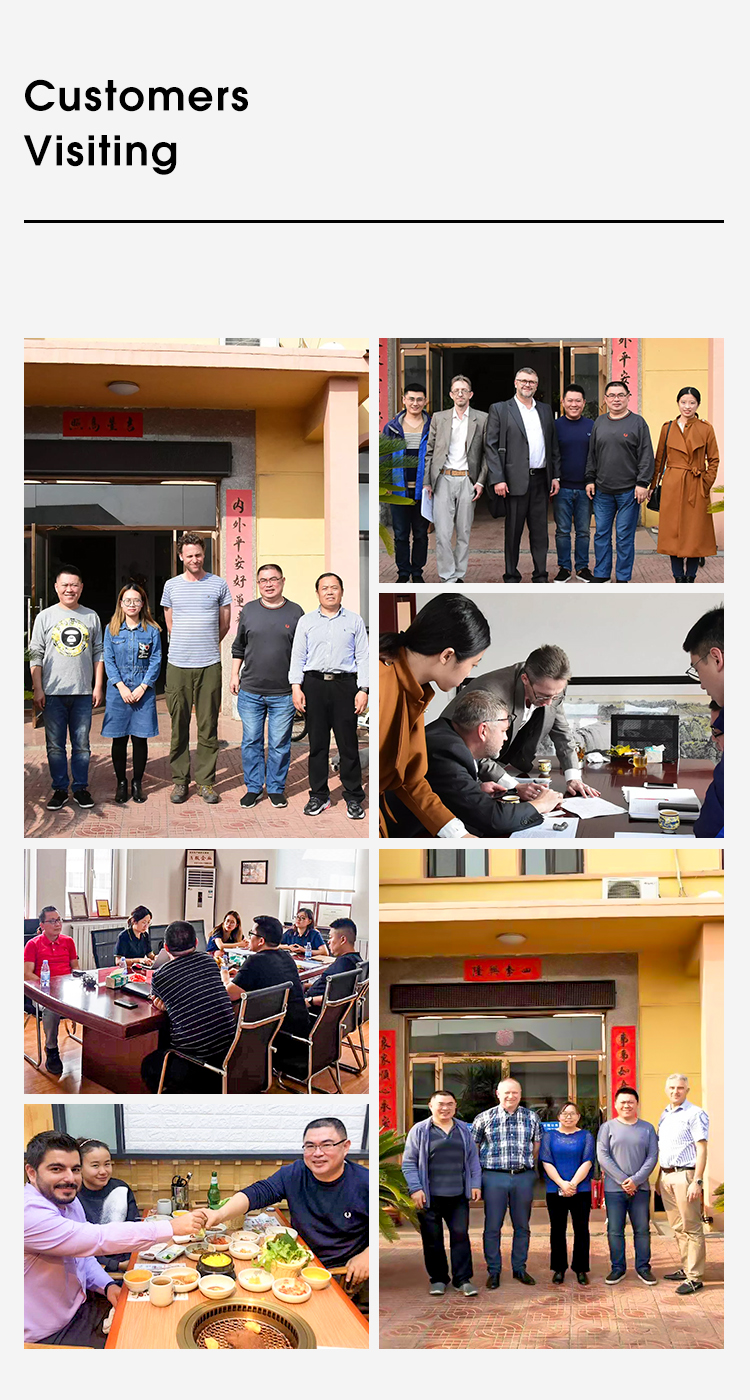
FAQ
1. Why is forged metal stronger than cast or machined metal? This stems from the grain flow caused through forging. As the metal is pounded the grains deform to follow the shape of the part, thus the grains are unbroken throughout the part. Some modern parts take advantage of this for a high strength-to-weight ratio. 2. What are the main difference between hot and cold forging? The cold forging manufacturing process increases the strength of a metal through strain hardening at a room temperature. On the contrary the hot forging manufacturing process keeps materials from strain hardening at high temperature, which results in optimum yield strength, low hardness and high ductility. Which forging method to apply is based on the required functions of the desired component, the industry and if it’s a mass production or a low volume of customized parts. 3. What’s the difference between forging and casting? Casting and forging are both described as taking metal material and making it into specific forms and shapes. However, the processes involved for forming that metal are very different. Casting requires the material to be in a molten state and then poured into a “cast” for the final shape. The forging process takes a bar or billet of material and heats it up to a high temperature without melting it; making the metal soft and malleable. It is then hammered or pressed into a specific shape in a closed-die by a hammer. 4. Why are iron and its alloys almost hot forged? This is for two reasons: 1) First, if work hardening were allowed to progress, hard materials such as iron and steel would become extremely difficult to work with. 2) Secondly, steel can be strengthened by other means than cold-working, thus it is more economical to hot forge and then heat treat. Alloys that are amenable to precipitation hardening, such as most alloys of aluminum and titanium, can also be hot forged and then hardened. Other materials must be strengthened by the forging process itself. 5. What is closed die forging? Closed die forging is a forging process in which dies move towards each other and covers the workpiece in whole or in part. The heated raw material, which is approximately the shape or size of the final forged part, is placed in the bottom die. The shape of the forging is incorporated in the top or bottom die as a negative image. Coming from above, the impact of the top die on the raw material forms it into the required forged form. 6. What’s the difference between open die forging and closed die forging? The technique of both open die forging and closed die forging is different. In general, for closed die forging, the molding dies are first precision machined and cost is high. The metal bars are then placed on between upper and lower dies and forged to any shapes needed. After closed die forging very less or no machining will be operated due to its high accuracy throughout the process. So closed die forging is also a net shape or near net shape process. For open die forging, enormous compressive forces are imposed by the continuous strike of a forging hammer to deform the metal billets. Unlike closed die forging, dies of open die forging is very simple. And secondly machining operation is always carried out.
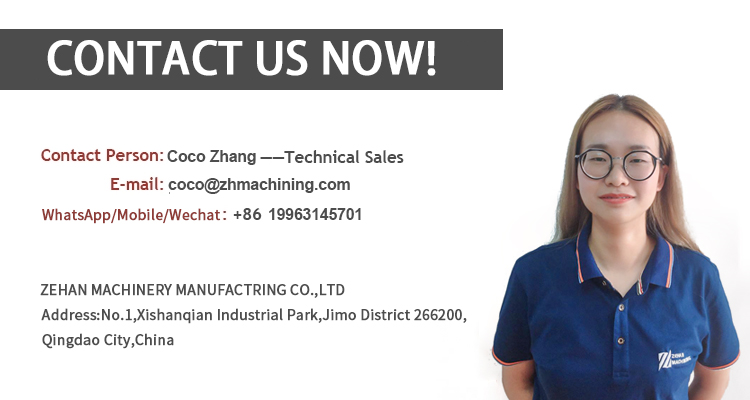
Product Categories : Sand Casting Parts > Sand Casting Parts
Premium Related Products
Other Products
Hot Products
Custom High Precision Casting Mercedes Benz Truck PartsFoundry Good Quality Precision Iron Casting for PumpOEM Precision Stainless Steel Die Casting Spin ManufacturerSupplier Custom Good Quality High Precision Steel CastingChina Foundry Custom High Quality Casting Aluminiumprecision aluminum die casting housing partzinc die casting clock frameDifferent kind of stamping partPart made by plastic injectionAluminum Die Casting Part with ISO9001die casting mould makingCNC machining partPar38 heatsinkAluminum die casting partDie casting partanodizing part